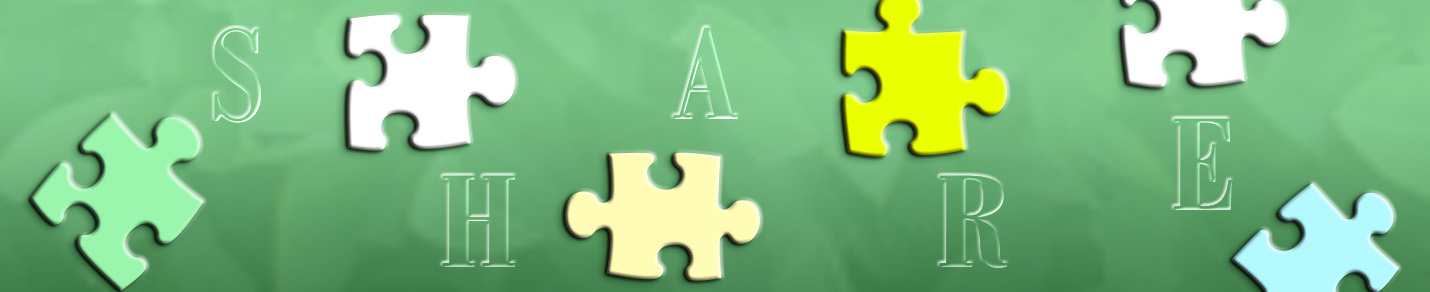
浪费始于设计
一个工厂、一个车间或者一条生产线的建设涉及到许多环节,其中设计工作因影响到项目投资额、生产安全性、产品品质、生产效率、系统稳定性和可靠性、后期运营成本等而显得非常重要。
然而,目前我国蒸汽系统的设计存在很多问题,造成投资浪费的同时,埋下了生产运行中设备效率低下、运行成本高和能源浪费等诸多隐患。长期调研发现,约80%的蒸汽用户存在较明显的系统设计问题。
这种案例可信手拈来,下面列举一、二:
案例一、某知名药企
该企业总用汽量不超过22吨/小时,锅炉出口压力为10barg,现场用汽压力以3barg为主。
根据生产需要,合理的设计应该是:从锅炉房架设3条DN150的管路到车间,然后通过5个DN125减压站(指减压站入口管径)减压后为各用汽点供汽。
实际情况是:从锅炉房到用汽车间铺设DN200管路3条、DN150的管路2条;在车间内共设置DN80减压站3个、DN100减压站1个、DN125减压站1个、DN150减压站6个共计11个减压站。
造成的损失和后果:管道、保温材料及安装的投资各增加至少100%;热量损失增大至少1倍;减压站的总投资也增加至少100%倍;系统含水量大,设备效率降低;管道、阀门、设备等的腐蚀加剧;系统停机率高,维修保养费用增加,系统寿命缩短;产品质量受到影响;生产运行安全性降低。
案例二、某食品加工企业
该企业刚建成不久。现场发现,从蒸汽产生、输送、使用等各环节都存在一些问题。其中,某一车间的分汽缸出口设置了4个DN100减压站,由8barg减压到3barg左右后向远处的设备供汽。
合理的设计应该是:一根DN125的管理输送8barg的蒸汽到用汽点,然后根据需要就地减压。
相比合理设计,实际情况导致的主要问题有:管道、保温及安装的费用增加大约300%;热能损失增大约3倍;减压站的总投资也增加约300%;设备入口蒸汽干度降低,设备效率降低。
在广大蒸汽用户中,类似的情形不胜枚举。许多项目的设计阶段就是浪费的开始,这种浪费包含设备投资、安装、运行、维护等短期投入和长期持续的浪费,也涉及能源的浪费,给企业造成极大的损失!
相反,优秀的设计方案不仅能为企业大幅降低建造投入,更是企业长期经济效益的坚实基础!因此,很大程度上,可以说,效益是设计出来的!